Colour & Print Solutions by the hubergroup: The colour BLACK
Carbon-Free Black Printing Inks – A Milestone for Sustainable Print Products?
In the graphic printing industry, black is at the top of the colour palette – whether in offset, flexographic, or digital printing. But conventional black inks typically contain carbon black, a pigment that is not only energy-intensive to produce but also significantly disrupts the paper recycling process.
What’s the Problem with Carbon Black?
Carbon black absorbs infrared light – and that’s exactly what optical sensors in recycling plants use to detect and sort printed materials. As a result, packaging or paper printed with carbon black-based inks cannot be properly identified and is sorted out incorrectly. The outcome: high-quality material is lost in the waste stream.
The Alternative: Carbon-Free Black Printing Inks
In recent years, research has focused on sustainable pigment alternatives – such as iron oxides, organic pigments, or biochar. These are often IR-transparent and therefore easier to sort.
Opportunities & Developments
• IR-readable black pigments: New formulations allow for deep black tones that look like classic black but are recycling-friendly.
• Digital printing & inkjet technology: Particularly open to new carbon-free pigments due to more flexible ink formulations.
• Offset printing: Greater challenges, as carbon black plays a key role in opacity and ink stability.
Implementation Challenges
• Colour intensity & opacity: Carbon-free black pigments must match carbon black in terms of quality and performance.
• Cost: Alternatives are currently more expensive – a barrier to widespread adoption.
• Print compatibility: Reformulating inks may require adjustments in drying behaviour and machine compatibility.
Benefits in the Recycling Process
• Improved detectability in NIR-supported recycling facilities
• Higher recovery rates of paper and packaging plastics
• Less waste, more circular economy
• Positive CO₂ balance, especially with pigments made from renewable resources
Conclusion
Carbon-free black printing inks are no longer a topic for the future – they are a necessary development for a functioning circular economy in the print and packaging sectors. We're still at the beginning, but innovations and collaborations along the entire value chain – from pigment manufacturers to printers and recyclers – offer hope.
Printing industry, be bold. Real sustainability starts with the right colour.
The petfood example below demonstrates an alternative solution, which can be to completely eliminate black and use a dark Pantone colour instead that does not contain carbon at all: Together with the supplier Partners in Petfood Netherlands and the printer Inn-Flex Italy, epda Member FroQ found this solution for their client Albert Heijn - Premium petfood.
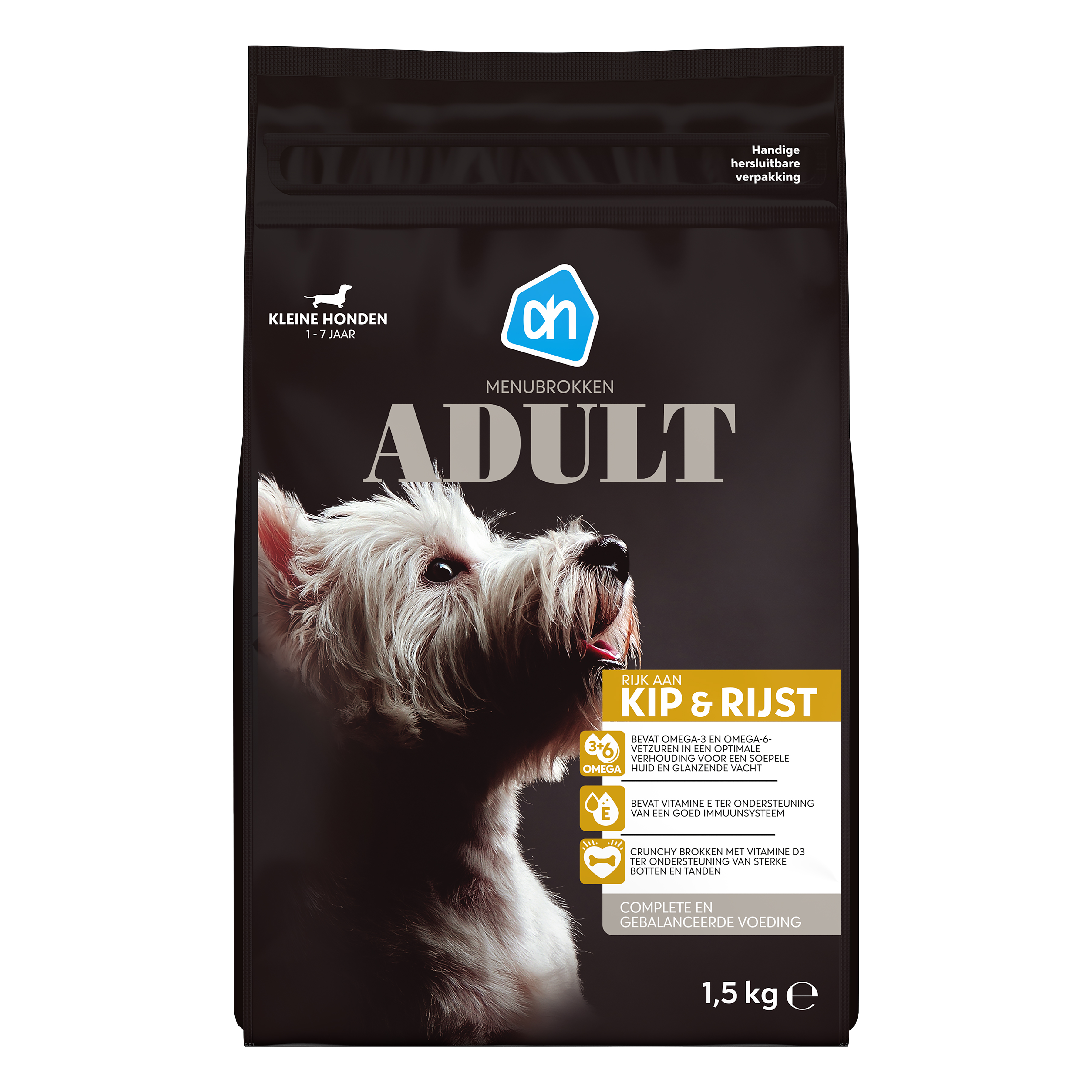
PPWR – Paper and Packaging Waste Regulation
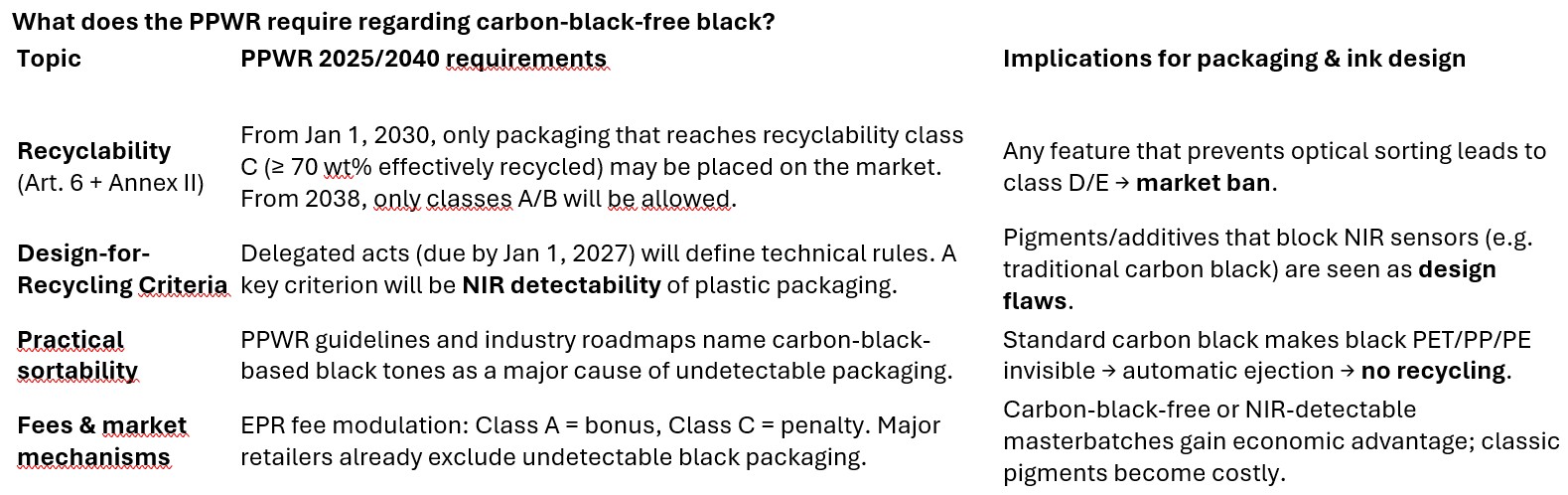
Summary
There is no explicit ban on carbon black pigments, but the functionality requirements effectively phase them out:
• If a black plastic packaging cannot be detected by NIR sorting, it will no longer be allowed in the EU starting 2030.
• By 2028, producers must provide proof of compliance with recyclability standards.
Recommended Actions
1. Switch to carbon-black-free or NIR-detectable blacks
Use masterbatches based on iron oxide, copper chromite, or similar alternatives.
2. Change the color tone
Deep greys, navy blues, or anthracite often match brand aesthetics and remain detectable.
3. Limit use to print only
Applying black ink (instead of coloring the entire plastic body) on light/transparent substrates keeps packaging detectable—especially if the ink covers less than 10% of the surface.
4. Ensure traceability
Test samples using NIR scanners or request certification from your masterbatch supplier. From 2028, compliance documentation is mandatory.
Practical Checklist for “Carbon-Free Black” Packaging
✅ Check your pigment composition: Is PBK 7 (carbon black) listed? If yes, seek alternatives.
✅ Measure NIR reflectance: Below 30% reflectance in the 1000–1700 nm band indicates risk.
✅ Conduct real-world tests: Submit samples to MRFs or PET sorting facilities.
✅ Evaluate EPR cost impact: Run cost simulations for switching vs. staying.
✅ Inform your value chain: Many retailers already require proof of NIR detectability—don’t wait until 2030.
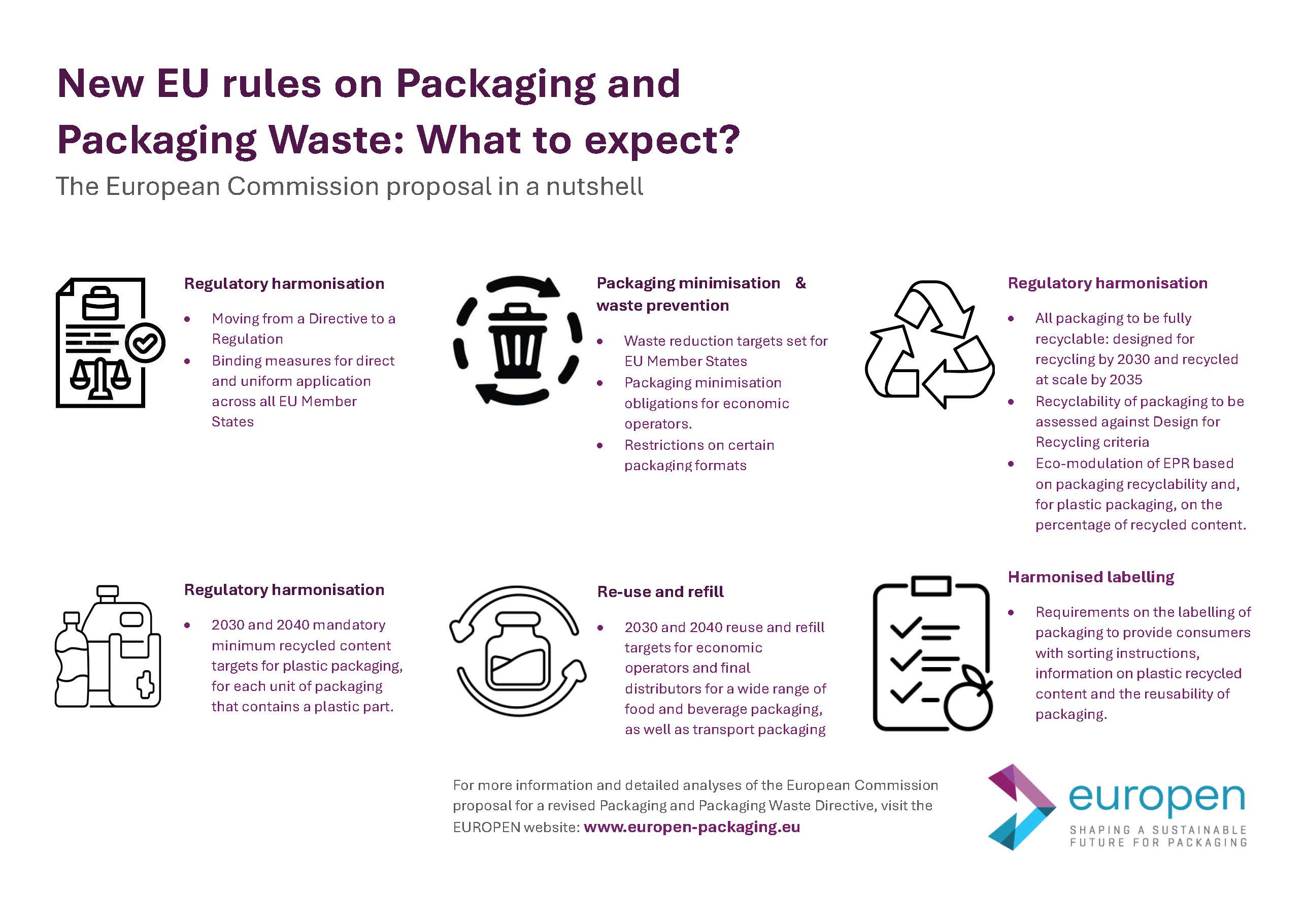